How Do 3D Printers Work? Step-by-Step Explained
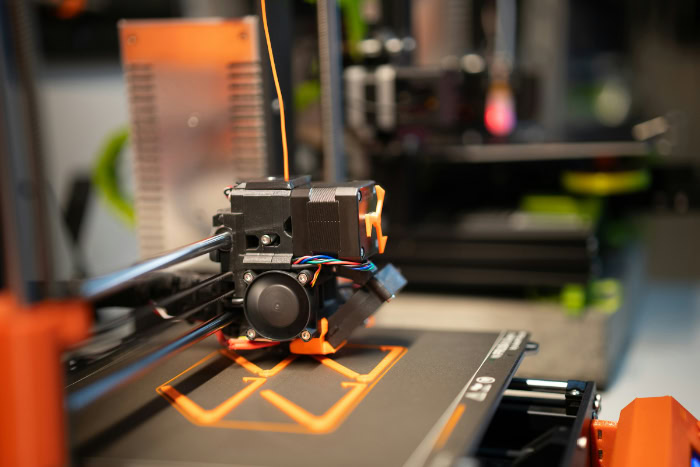
Once considered futuristic, 3D printing has become a force of change across industries from manufacturing to medicine and even home workshops. With the press of a button, intricate objects can be created from a digital design, transforming raw materials into everything from car parts to dental implants and creative art pieces.
This technology invites individuals and businesses alike to reimagine how products are made, customized, and brought to life.
Core Principles of 3D Printing
At its foundation, 3D printing relies on simple yet groundbreaking concepts that distinguish it from traditional fabrication techniques. Instead of removing material from a solid block, 3D printing builds objects up, layer by layer, following detailed digital instructions.
This approach not only changes how items are produced but also allows for innovative shapes, faster prototyping, and greater customization.
Additive vs. Subtractive Manufacturing
Traditional manufacturing methods, such as CNC machining or milling, shape objects through subtraction. Imagine starting with a solid chunk of metal or plastic and cutting away sections until the desired form emerges.
This process can create significant material waste and often limits the geometric complexity of the final product.
By contrast, 3D printing takes an additive approach. Rather than carving from a block, a 3D printer deposits material only where it is required.
Each layer stacks upon the last, forming the intended shape with remarkable efficiency. Additive manufacturing significantly reduces excess material and enables the creation of complex internal structures or designs that would be nearly impossible to achieve through subtraction alone.
Layer-by-Layer Fabrication
The secret behind a 3D printer’s ability to create detailed and intricate items lies in its stepwise construction process. Starting from the bottom, the printer lays down thin sheets of material, one after another, guided by a digital blueprint.
Each layer, often thinner than a sheet of paper, bonds or fuses to the previous one. Gradually, the object takes shape vertically until completion.
This method opens the door to a vast world of possibilities. Designers can experiment with hollow components, internal channels, or mesh-like frameworks, all while maintaining strength and reducing weight.
The precise control over each layer also means that surface textures and fine details can be carefully customized, offering both functional and aesthetic advantages.
Digital-to-Physical Workflow
Every 3D printed object begins its life as a digital model. Using computer-aided design (CAD) software, creators develop three-dimensional representations of their intended objects.
These files serve as the essential blueprints for the printing process, ensuring accuracy and repeatability.
Before printing begins, software slices the digital model into horizontal cross-sections, translating the design into precise instructions for the printer. The finished product reflects every detail encoded in the CAD file, from its overall form to its most intricate features.
Thanks to this digital-to-physical workflow, rapid prototype iterations and custom designs become straightforward, making 3D printing a uniquely flexible tool for creators worldwide.
Key 3D Printing Technologies
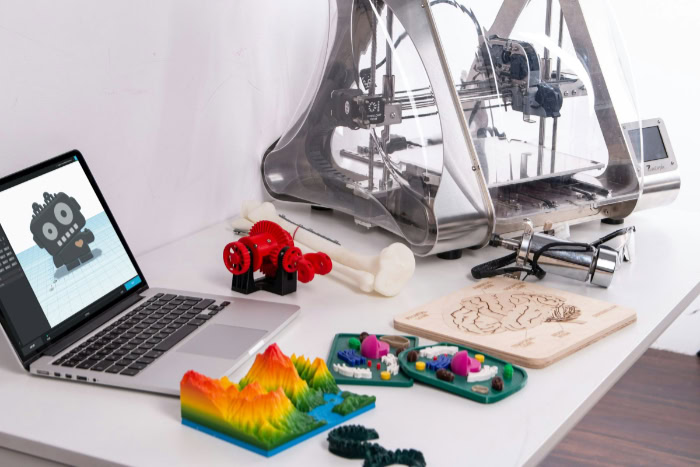
Modern 3D printing offers several technologies, each with unique strengths and ideal applications. From creative home projects to producing functional parts for aerospace or medicine, different printing methods have emerged to serve a variety of needs.
Examining the most prominent technologies helps clarify how objects are formed and highlights the remarkable versatility of 3D printing.
Fused Deposition Modeling (FDM)
Fused Deposition Modeling stands as one of the most accessible and popular 3D printing methods available today. The process starts with a spool of plastic filament, such as PLA or ABS, which is fed into a heated nozzle.
As the filament melts, the printer’s nozzle moves along precise paths, depositing fine threads of plastic layer by layer onto a build platform. Gradually, the object rises as successive layers fuse together.
Many people encounter FDM printers in classrooms, maker spaces, and home workshops. The technology serves as an affordable entry point for education, hobbyists, and rapid prototyping for engineers.
Simple operation paired with readily available materials makes it a go-to choice for creating everything from gadgets and replacement parts to detailed prototypes and artistic models.
Stereolithography (SLA)
Stereolithography takes a different approach, utilizing liquid resin as its starting material. Within the printer’s vat, a platform rests just below the surface of a photopolymer resin.
A focused ultraviolet laser traces each cross-section of the object, curing the resin and solidifying it into precisely shaped layers. As each layer finishes, the platform lowers slightly, and the next layer is formed directly on top.
SLA printers excel at producing objects with fine details and exceptionally smooth surfaces. Precision makes this technique a favorite among dental professionals, jewelers, and creators of medical models.
Components with intricate geometries, delicate textures, or tight tolerances benefit especially from the sharp accuracy delivered by Stereolithography.
Selective Laser Sintering (SLS)
Selective Laser Sintering harnesses the power of lasers and powdered materials to unlock design freedom. The process works by spreading a thin layer of powder, such as nylon or metal, across the build chamber.
A high-energy laser then scans the surface, fusing particles only in areas defined by the digital design. Once one layer is complete, the machine adds a fresh coat of powder, repeating the process until the object is fully formed.
An advantage of SLS lies in its self-supporting nature. Since the unused powder surrounds each part, additional structures are rarely needed, making it possible to print complex interlocking or moving parts in a single build.
Industrial designers turn to SLS for durable prototypes, functional components, and customized items in sectors where strength and precision matter, from automotive to medical devices. Metal-compatible versions of this technology have opened exciting opportunities in high-performance engineering and manufacturing.
Materials Used in 3D Printing
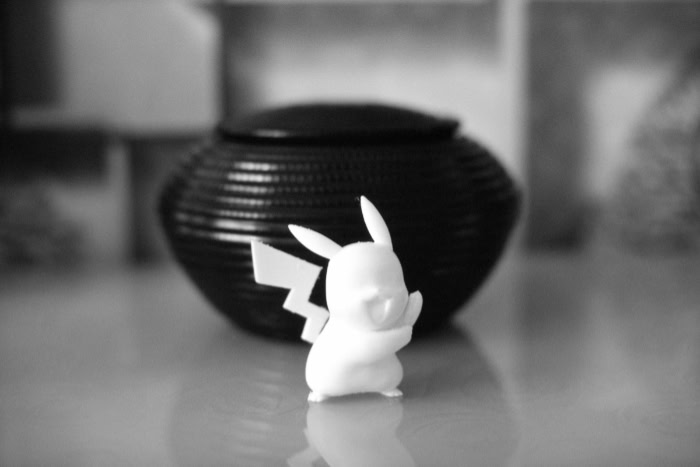
Material choice sits at the heart of what makes 3D printing so adaptable across different fields. From everyday objects created by hobbyists to industrial parts trusted in high-stress environments, the spectrum of available materials continues to expand.
The combination of material properties and printing technology dictates not only the appearance and function of the printed object but also its cost, durability, and practical use.
Plastics (PLA, ABS)
Plastics play a leading role for good reason. Two of the most commonly used filaments are PLA (Polylactic Acid) and ABS (Acrylonitrile Butadiene Styrene).
PLA is recognized for being user-friendly, biodegradable, and affordable, making it ideal for prototypes, toys, and decorative items. Its low melting point suits home printers and classroom projects, but it may not handle high temperatures or strong impacts well.
ABS, on the other hand, provides greater strength and better resistance to heat. It can withstand more demanding applications, such as mechanical parts or enclosures, and accepts post-processing techniques like acetone smoothing.
Both materials offer flexibility in color and finish, allowing users to balance printability with the needs of the final object.
Resins
For projects requiring detailed precision or a flawless surface, resin-based printing becomes the preferred choice. Liquid photopolymer resins, used mainly in SLA and similar technologies, can capture extremely fine features and produce models with smooth, almost glass-like textures.
This capability is especially useful for jewelry, dental models, miniatures, and prototypes where surface quality matters most.
Resins also come in specialized formulations designed for strength, transparency, or high-temperature resistance, meeting specific functional requirements that traditional plastics may not fulfill. The downside often relates to handling and safety, as liquid resins require careful storage, equipment cleaning, and protective gear during use.
Metals (Titanium, Steel)
Metals have brought 3D printing firmly into the industrial spotlight, expanding its use to applications once thought unprintable. Processes such as Selective Laser Sintering and similar techniques allow for the fabrication of parts in stainless steel, titanium, aluminum, and specialized alloys.
The resulting objects can meet high standards of durability, heat resistance, and mechanical performance.
Aerospace engineers, surgeons, and automotive designers benefit from the ability to produce lightweight, strong components and highly customized medical implants. Metals also allow for intricate internal structures, which would be impossible or too costly using traditional casting or machining.
Material Selection Criteria
Choosing the right material involves more than just matching a color or surface finish. Designers and engineers consider strength, flexibility, and compatibility with the intended environment.
For example, an object exposed to sunlight may require UV-resistant material, while a load-bearing mechanical part needs high tensile strength or impact resistance.
Temperature tolerance also factors into decisions, especially for components used in engines or electronic devices. Chemical resistance, ease of post-processing, and cost further shape what material best suits each 3D printing project.
The ability to select from such a diverse range of options makes 3D printing valuable not only for experimentation but for practical solutions in everyday life and advanced industries alike.
The 3D Printing Workflow: Step by Step
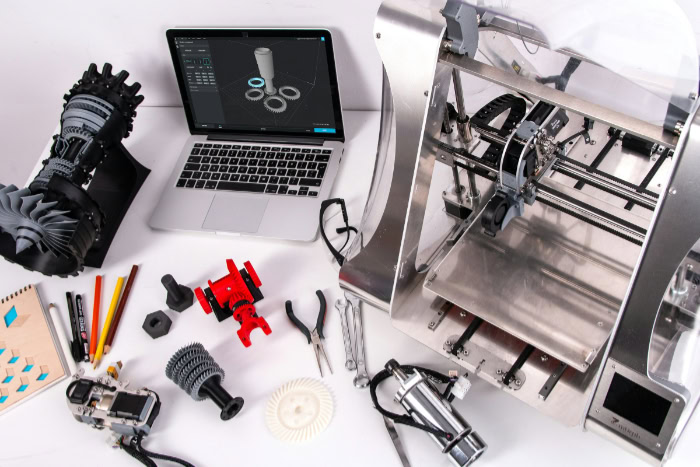
Transforming a digital idea into a tangible object with 3D printing involves more than simply pressing “print.” Each stage of the process contributes to the quality, precision, and success of the final product. From initial design to the finishing touches, attention to detail is critical.
Design Phase
Every 3D print starts as a digital design. Most creators use computer-aided design (CAD) software to craft a three-dimensional model.
For those just starting, intuitive programs like Tinkercad make it easy to create basic structures and shapes. More advanced users often turn to powerful options such as Fusion 360, which allows for complex assemblies, fine adjustments, and detailed technical drawings.
Not everyone prefers to design from scratch. Online repositories such as Thingiverse or Printables offer thousands of ready-made models available to download.
These files, typically in STL or OBJ format, can be quickly imported into the workflow, saving time and making the technology accessible for users of all skill levels.
Slicing Software
The next step translates the digital model into detailed instructions the printer can follow. Slicing software breaks the object into layers and converts it into G-code, a language that directs the printer’s movements.
Adjustments made within the slicer-such as layer height, print speed, infill density, and support structures-determine not only the final appearance but also the strength and weight of the printed piece.
Slicing software like Ultimaker Cura or PrusaSlicer provides a visual preview of each layer, allowing users to check for errors before printing begins. Fine-tuning these settings requires some experimentation, especially when balancing speed with print quality and material use.
Printing Process
With the G-code ready, the printer takes over. Before launching a print, careful calibration ensures the nozzle sits at the correct height and the print bed is level.
Failing to calibrate properly can lead to adhesion problems or uneven layers, impacting the finished piece.
Once the machine heats the print bed and extruder (or prepares the resin or powder, depending on the technology), it starts constructing the object layer by layer. Throughout the print, monitoring progress helps catch issues such as clogs, shifting, or warping before they ruin hours of work.
Larger or more complex objects may require several hours-or even days-to complete, so patience and vigilance go a long way.
Post-Processing
Finishing does not end when the printer stops. Many prints benefit from post-processing techniques to reach their full potential.
Simple methods include removing support structures, sanding rough surfaces, or trimming stray threads. More advanced forms of finishing involve painting parts for color and realism or using chemical baths to smooth surfaces, particularly for ABS prints.
Cleaning, curing, or assembling components adds another layer of craftsmanship. For resin prints, careful rinsing and additional curing under UV light ensure strength and stability.
Taking time with these finishing steps transforms each print from a basic prototype into a polished and functional object.
Applications and Practical Considerations
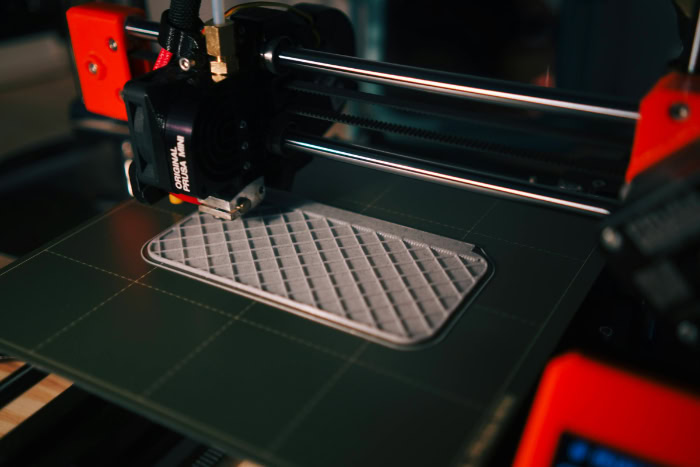
As 3D printing matures, its influence stretches far beyond its origins in prototyping labs. Today, the technology offers powerful solutions for industries ranging from healthcare to construction, while also presenting unique challenges.
The practical uses are inspiring, yet factors such as material capabilities and user expertise continue to shape how widely and effectively 3D printing can be adopted.
Benefits
Speed and flexibility stand at the forefront of 3D printing’s appeal. Rapid prototyping allows engineers and designers to move from a concept to a tangible prototype in a matter of hours or days.
Design iterations can be tested, tweaked, and reprinted with minimal downtime, accelerating innovation across fields such as product development, consumer electronics, and creative arts.
Healthcare has embraced 3D printing for its capacity to personalize. Prosthetics, dental aligners, and even implants can be customized with precise patient data, leading to better fit and comfort.
Surgeons benefit from anatomical models that match a patient’s unique structure, allowing for more accurate planning and improved outcomes. The technology’s ability to cater to individual needs has helped reshape patient care and medical device production.
Challenges
Despite its promise, 3D printing is not without obstacles. Material selection remains a significant limitation; for example, some common plastics, like PLA, can be brittle or unsuitable for parts requiring high strength or flexibility.
Although advancements in materials science continue, users often need to balance cost, durability, and performance.
Skill requirements present another challenge. Success in 3D printing often depends on knowledge of design software, printing hardware, and post-processing techniques.
Inadequate calibration, file preparation, or troubleshooting can lead to wasted time and resources. Education and experience are crucial for unlocking the full capabilities of the technology.
Real-World Examples
Automotive companies have adopted 3D printing to develop lightweight, custom parts that meet strict performance standards. The ability to manufacture replacement components or design intricate geometries gives engineers opportunities to reduce weight and improve efficiency in vehicles.
Car enthusiasts also benefit, as rare or discontinued parts can be recreated on demand.
In the construction sector, large-scale 3D printers now produce entire building sections or even complete houses. Concrete and advanced composite materials are deposited layer by layer, offering faster build times and less material waste compared to traditional methods.
Such innovation holds promise for affordable housing, disaster relief, and creative architectural designs.
The expanding list of applications continues to demonstrate how 3D printing can be adapted to solve complex challenges while enabling creative solutions across fields. From functional prototypes to life-changing medical devices and cutting-edge architecture, the limits of what can be built are being redefined.
Conclusion
3D printing stands as a powerful force making manufacturing more accessible and flexible than ever before. Its ability to turn digital ideas into real-world objects, one layer at a time, is reshaping everything from product design and healthcare to architecture and daily problem solving.
With a range of technologies and materials to choose from, both individuals and industries can benefit, regardless of experience level or scale. Curiosity and a willingness to experiment open up endless creative opportunities, making now an ideal time to explore what 3D printing can offer for personal projects or professional breakthroughs.