What Is Thermal Paste? How It Improves Heat Transfer
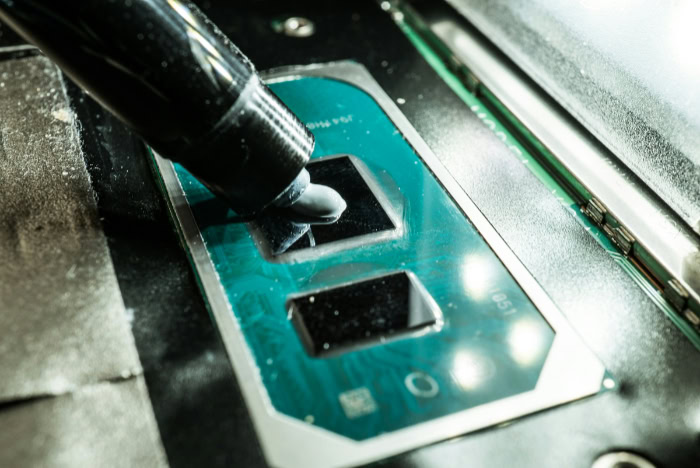
Effective cooling is vital to ensuring the smooth operation and longevity of modern electronics. CPUs and GPUs generate significant heat during use, and managing this heat is essential to prevent performance issues or hardware damage.
Thermal paste plays a crucial role in this process, serving as the bridge that facilitates efficient heat transfer between processors and their cooling systems. Without it, air gaps between surfaces can lead to overheating, throttled speeds, and even permanent hardware failure.
Definition And Core Function
Thermal paste, also referred to as thermal grease or compound, is a specialized material designed to improve the thermal conductivity between two surfaces. It is applied between the heat-producing unit (such as a CPU or GPU) and the heatsink, which is responsible for dissipating heat.
Its composition typically includes silicone or oil-based substances mixed with thermally conductive materials like metal particles (such as silver or aluminum), ceramic particles, or even carbon-based elements. The specific materials used in its formulation determine its effectiveness in conducting heat.
The paste’s semi-liquid form allows it to fill in uneven surfaces and microscopic imperfections, ensuring maximum contact between the processor and the heatsink. This increases the efficiency of the heat transfer process, reducing the risk of overheating and extending the lifespan of the hardware.
Primary Purpose
The primary function of thermal paste is to eliminate thermal resistance caused by air gaps. Even though CPUs, GPUs, and heatsinks appear smooth to the naked eye, they have tiny imperfections that prevent perfect contact when placed together.
These gaps trap air, which is a poor conductor of heat, and can severely hinder the cooling system’s effectiveness.
By filling these gaps, thermal paste creates a continuous and efficient pathway for heat to move from the processor to the heatsink, where it can then be dissipated into the surrounding environment. This process prevents temperature spikes that can lead to issues like thermal throttling, where the processor speed is reduced to manage heat, or even permanent damage to the hardware.
Proper application of thermal paste is therefore essential for ensuring stability and performance in electronic devices.
Composition, Types, And Performance
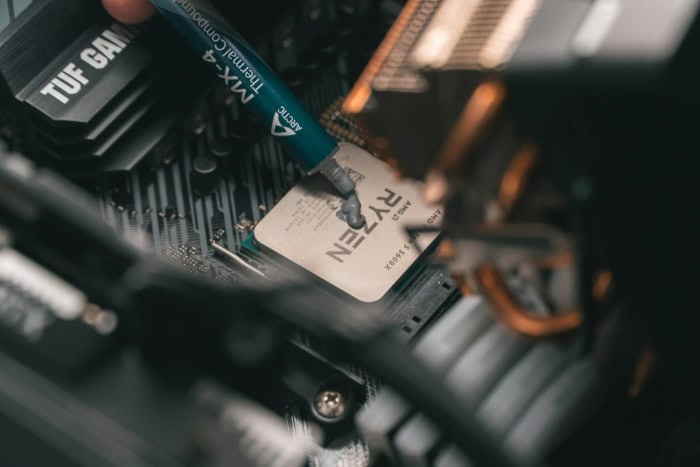
The effectiveness of thermal paste depends heavily on its composition, which directly impacts its thermal conductivity, durability, and ease of application. As a specialized material designed to enhance heat transfer, thermal paste comes in several distinct types, each suited to different performance requirements and use cases.
Selecting the right type involves understanding the thermal paste’s core materials and their properties, as they can influence not only the cooling efficiency but also the risks and maintenance involved.
Common Materials
Thermal paste is formulated using a base, typically silicone or oil for stability and texture, combined with thermally conductive particles that allow heat to flow efficiently. Among these particles, three primary categories are commonly used:
Metal-based thermal pastes are widely recognized for their exceptional heat conductivity. Materials like silver, aluminum, and copper are blended into the compound to provide superior thermal performance, making them popular among overclockers and users requiring maximum cooling efficiency.
However, metal-based pastes are electrically conductive, which introduces the risk of short circuits if mishandled during application.
Ceramic-based thermal paste is an alternative favored for its ease of use and safety. The formula incorporates fine ceramic particles that effectively transfer heat while remaining non-conductive.
Unlike metal-based options, ceramic-based pastes eliminate the risk of accidental electrical contact, making them ideal for less experienced users or applications where safety is paramount.
Liquid metal thermal pastes represent the pinnacle of heat transfer capability, offering unmatched conductivity for demanding tasks such as extreme overclocking. However, their metallic nature makes them tricky to apply, and they are not compatible with aluminum heatsinks, as they can cause corrosion.
These factors make liquid metal more suited to advanced users who prioritize thermal performance above all else.
Thermal Conductivity Values
The thermal conductivity of thermal paste is typically measured in watts per meter-kelvin (W/mK), which reflects its ability to conduct heat effectively. Basic pastes often fall within the 2 to 5 W/mK range, providing adequate cooling for general-purpose use.
For higher-performance needs, such as gaming or heavy workloads, premium pastes with conductivity values above 8 W/mK may be preferred. Liquid metal options stand out in this regard, achieving ratings as high as 13 W/mK, far surpassing standard offerings.
Understanding these conductivity ranges allows users to match the thermal paste to the demands of their system, ensuring optimal heat transfer and performance under various conditions.
Durability Factors
Durability is another critical factor when evaluating thermal paste, as its consistency and effectiveness can degrade over time. Organic formulas, which rely on oil or silicone bases, tend to dry out faster, especially under high temperatures.
This drying process can reduce their effectiveness, necessitating more frequent reapplication.
Non-organic formulas, on the other hand, are designed for long-term stability. They resist drying and maintain their consistency for extended periods, making them ideal for users who prefer low-maintenance solutions.
Liquid metal pastes, while durable, require specific precautions during application and periodic checks to ensure optimal performance.
Choosing a durable paste can reduce the frequency of maintenance while providing consistent cooling over time, making it an important consideration for both casual users and enthusiasts.
Application Techniques And Best Practices
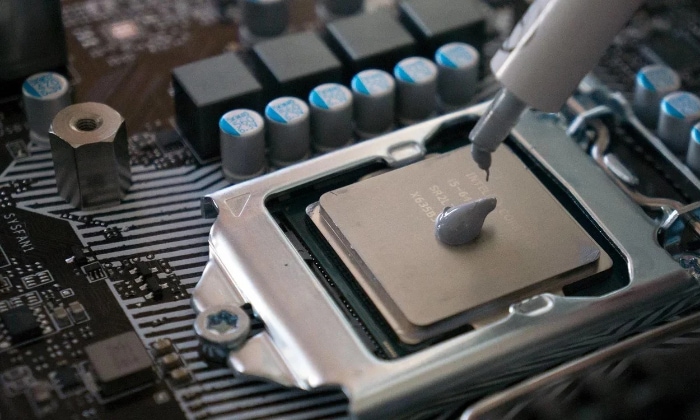
Applying thermal paste correctly is essential for ensuring effective heat transfer between processors and their cooling solutions. Improper application can lead to suboptimal cooling, overheating, and reduced hardware longevity.
While the process may seem straightforward, certain techniques, precautions, and methods play a critical role in achieving ideal results.
Preparation
Before applying thermal paste, preparation is a critical step that ensures a clean and smooth mating surface. Residual paste from previous applications, dust, and grime can disrupt heat transfer and affect cooling performance.
Cleaning both the processor and heatsink surfaces thoroughly with isopropyl alcohol is recommended. This removes old paste and contaminations, leaving a pristine surface for the new application.
Using a lint-free cloth or paper helps prevent fibers from sticking to the cleaned surfaces, ensuring the paste adheres evenly.
Rushing this step or neglecting surface cleaning can trap impurities between components, reducing the effectiveness of even high-quality thermal paste. Careful preparation lays the foundation for optimal application and heat transfer.
Application Methods
The method chosen for applying thermal paste often depends on the processor size and shape, as well as personal preference. For most CPUs and GPUs, the pea-sized dot method is a reliable and widely used technique.
A small dot of thermal paste is placed at the center of the processor, and pressure from the heatsink spreads it evenly across the surface when installed. This approach minimizes excessive paste usage, ensuring an even layer without waste or mess.
For larger processors, such as those used in server-grade equipment, the line or spread method may be more suitable. The line method involves placing a thin strip of paste down the middle of the processor, while the spread method uses tools to manually distribute the paste across the surface.
Both methods aim to cover the mating area completely without over-application, which can lead to seepage or reduced effectiveness.
Regardless of the chosen method, uniform coverage is key to eliminating air gaps and ensuring a smooth transfer of heat.
Common Mistakes
Errors during thermal paste application can compromise the cooling process and lead to performance issues. Using too much paste is one of the most frequent mistakes, as excess material can spread beyond the intended area when the heatsink is installed.
This can create messes, impede heat transfer, and—if using electrically conductive paste—pose a risk to nearby circuitry.
Applying too little paste is another common error, as inadequate coverage fails to eliminate air pockets, reducing overall cooling efficiency. Precision in quantity and placement ensures that the paste performs as intended.
Another oversight involves neglecting to reapply paste after removing the cooling solution. Removing the heatsink often disrupts the seal created by the paste, and reusing old paste can lead to uneven coverage or degraded conductivity.
Always clean and reapply paste when reassembling cooling systems to maintain optimal thermal performance.
Choosing And Maintaining Thermal Paste
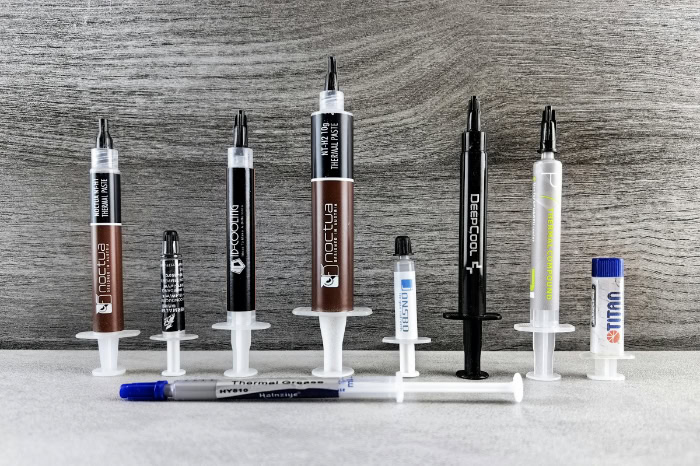
Selecting the right thermal paste and maintaining its effectiveness over time are crucial for ensuring stable hardware performance. With an array of options available, users must consider their performance needs, safety preferences, and long-term reliability.
Additionally, even high-quality thermal paste requires proper care and periodic reapplication to maintain its thermal efficiency.
Selection Criteria
Thermal paste varies significantly in terms of performance levels, compatibility, and safety features, making the selection process an important part of optimizing cooling systems. Users should first evaluate their performance needs based on how they plan to use their hardware.
For general-purpose setups, ceramic-based thermal paste often provides sufficient conductivity while remaining simple and safe to apply. Gaming systems and moderately overclocked CPUs can benefit from high-performance metal-based pastes, which deliver greater thermal conductivity but require more caution due to their electrical conductivity.
Advanced overclocking or systems requiring maximum heat dissipation, such as high-end gaming rigs or workstations, may call for liquid metal thermal paste, which offers unmatched conductivity. However, liquid metal pastes should only be used by experienced users, as they are electrically conductive and incompatible with aluminum heatsinks.
Safety preferences are another critical factor, especially for those less experienced or working in environments with sensitive hardware. Non-conductive options like ceramic-based pastes remove the risk of electrical shorts, making them suitable for most users.
Carefully weighing performance gains against application risks ensures both efficiency and safety when choosing a thermal paste.
Maintenance Tips
Thermal paste degrades over time, requiring regular maintenance to preserve its ability to transfer heat effectively. Reapplication is generally recommended every two to five years, depending on the type of paste and usage conditions.
Organic pastes, which are prone to drying out faster, may need to be replaced more frequently, while non-organic formulas designed for long-term stability offer extended intervals between applications.
Monitoring system temperatures can help detect signs of thermal paste degradation. Gradually increasing temperatures under normal usage may indicate that the paste is drying out or losing its effectiveness, prompting the need for replacement.
Regular checks ensure that cooling systems remain efficient and prevent overheating issues from arising unexpectedly.
Proper reapplication involves cleaning off the old paste completely and applying a fresh layer using proven techniques to achieve optimal coverage. Neglecting this maintenance step can lead to reduced cooling efficiency and potential system instability over time.
Debunking Myths
Misconceptions about thermal paste can lead to poor application practices or unnecessary concerns. One common myth is that using more paste improves cooling performance.
Excess paste often causes messes and can even trap air pockets rather than eliminate them, reducing overall heat conductivity. A precise and measured application is far more effective than piling on extra material.
Another myth suggests that all thermal pastes dry out over time. While this is true for many organic formulas, non-organic pastes are specifically designed to maintain their consistency and performance for extended periods.
Understanding the properties of various paste types can help dispel doubts about durability and allow users to choose products suited to their long-term needs.
Conclusion
Thermal paste serves as an essential component in electronics cooling, bridging the gap between processors and heatsinks to facilitate efficient heat transfer. By filling microscopic imperfections and eliminating air pockets, it plays a significant role in preventing overheating, maintaining performance stability, and protecting hardware from potential damage.
Whether used in basic systems or high-performance setups, thermal paste ensures that critical components operate within safe temperature limits.
Proper selection, application, and maintenance of thermal paste are crucial for maximizing its effectiveness. Choosing the right type of paste based on performance needs and safety considerations allows users to achieve optimal cooling results.
Accurate application techniques, paired with regular monitoring and reapplication when necessary, ensure that the paste continues to perform as intended over time. By paying attention to these aspects, users can maintain the reliability and longevity of their electronics, enabling them to perform at their best.
Thermal paste may be a small component, but its impact on a system’s stability and efficiency is undeniable.